在鑄造生產領域,鑄件液壓拉力試驗機是評估金屬材料強度與韌性的核心設備。其工作原理基于液壓傳動技術與精確的力學測量方法,通過系統性測試揭示材料的內在性能。
一、核心構造與工作流程
鑄件液壓拉力試驗機由主機、液壓系統、測控系統和安全防護裝置四部分構成。主機采用雙立柱框架結構,夾持系統配備液壓自動對中裝置,確保試樣軸向受力均勻。液壓系統作為動力核心,以22MPa工作壓力驅動活塞產生200噸最大試驗力,通過伺服閥實現力值精準控制。壓力傳感器與位移編碼器實時采集數據,經A/D轉換后由工控機進行數據處理,最終生成應力-應變曲線。
測試時先將鑄造試樣(標準尺寸如φ10×50mm棒材)置于夾持鉗口中,通過液壓加載系統以5-500mm/min可調速度施加拉力。試樣在持續增大的拉力作用下產生彈性變形,當應力超過材料屈服極限后逐漸出現頸縮現象,最終發生斷裂。系統同步記錄載荷峰值與延伸率等關鍵數據。
二、關鍵技術指標解析
1.負荷測量系統:采用輪輻式負荷傳感器,分辨率達0.5N,經三級標定確保測量精度在±0.5%FS內。溫度補償裝置消除環境溫度變化對測量結果的影響(0.5-45℃工作范圍)。
2.位移測量系統:配置雙光柵尺測量裝置,位移測量精度±0.002mm,配合應變放大器實現微小變形的高精度監測。
3.自動化控制:采用閉環PID控制算法,響應時間<50ms,可維持±1%的載荷控制精度。具備自動調零、過載保護、緊急停機三重安全防護機制。
特殊工藝鑄件可選用高溫(1200℃)或腐蝕環境(鹽水、酸堿)專用夾具進行測試。某鑄鋼企業通過該設備發現球墨鑄鐵試樣在應力循環10^4次后開始出現微裂紋,及時調整了合金配比,使產品疲勞壽命提升3倍以上。
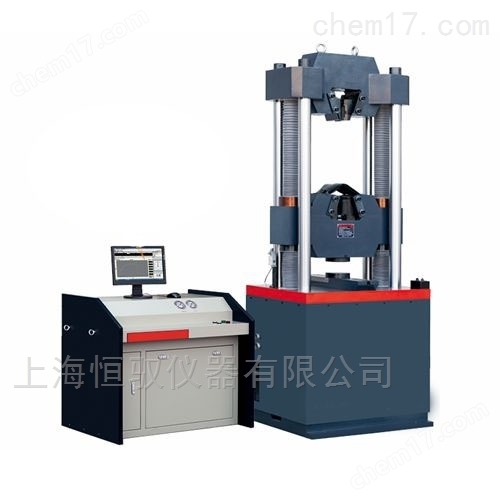
鑄件液壓拉力試驗機通過精確量化材料極限承載能力,為鑄造工藝優化提供科學依據。隨著智能傳感與數字孿生技術的融合,該設備正向著自適應測試與云數據管理方向發展,推動鑄造行業向精密制造邁進。